تکنولوژی رسوبزدایی هیدروفلو در کلیه مبدل های حرارتی آب به آب، آب به هوا، بخار به آب
تکنولوژی رسوبزدایی هیدروفلو در کلیه مبدلهای حرارتی آب به آب، آب به هوا، بخار به آب قادر است رسوب گیری و رسوب زدایی از رسوبات ناشی از سختی آب جلوگیری نموده در رسوبات قدیمی کربناتی و سیلیکاتی را نیز به مرور زمان تمیز نماید. تغییر دمای آب و افزایش آن موجب کاهش حلالیت یونهای سختی موقت، کربنات و بی کربنات کلسیم و منیزم میگردد یونهای آزاد شده بلافاصله به سطوح فلزی مبدلهای حرارتی چسبیده و تشکیل رسوبات سخت کربناتی میدهند. رسوب همانند عایق عمل میکند و مانع از انتقال حرارت سریع میشوند. در مبدلهای حرارتی هوا هر یک میلیمتر رسوب آب سخت حداقل 8 الی 10 درصد انتقال حرارت را کاهش میدهد. تشکیل رسوب سخت و تجمع یونها بر روی سطوح موجب جذب بسیار سریع سایر املاح رسوبات موجود در آب میگردد و ضخامت رسوب به سرعت افزایش مییابد و نهایتا موجب مسدود شدن تیوب ها و مسیر عبور آب میشود. افت فشار ایجاد شده توسط رسوبات آب سخت موجب افزایش مصرف انرژی الکتریکی در الکترو پمپها میشود. اگر به دنبال راه کار دائمی، آسان و کم هزینه جهت برطرف کردن مشکل سختی آب، رسوب گیری مبدلها و سختی گیری در تجهیزات هستید و از اسید شویی دائمی مبدلهای حرارتی و سرویس مداوم سختی گیرهای و هدر رفت آب در سختی گیرهای رزینی خسته شدهاید ، تکنولوزی سبز هیدروپت با دستگاه های رسوبزدایی هیدروفلو بهترین راهکار غیر شیمیایی جهت مقابله با رسوب و سختی آب است.
محصولات مرتبط :
رسوب زدای سری C
رسوب زدایی مبدلهای روغن هیدرولیک سیمان ممتازان کرمان
به طور کلی رسوب در کارخانجات سیمان به یک معضل غیر قابل حل و مستهلک کننده تجهیزات تبدیل شده است. هزینه رسوب زدایی و سختی گیری آب در کارنجات صنعتی نظیر تولید سیمان بسیار بالا است. نیاز متوسط به 1200 الی 1500 مترمکعب آب سختی گیری شده در شبانه، رقم قابل توجهی است. از سوی دیگر رهاسازی 150 تا 250 مترمکعب آب فوق اشباع از نمکهای معدنی، کربناتها و سدیم آسیب جبران ناپذیری به سفرههای آب زیرزمینی وارد مینماید. شور شدن آبهای زیرزمینی، کاهش کیفیت آبهای استحصالی از چاههای عمیق را در فاصله زمانی بسیار کوتاه به دنبال دارد.
کارخانه سیمان ممتازان کرمان که رکورد طراحی تا ساخت یک کارخانه سیمان در ایران را یدک میکشد در آذرماه ماه 1390 اقدام به تجهیز واحد آسیاب سیمان با دستگاههای رسوب زدای هیدروفلو نمود. آسیابهای سیمان کارخانه از نوع گلولهای هستند و واحد آسیاب سیمان دارای دو آسیاب گلولهای است. تجهیزات خنک کننده آسیاب سیمان شامل مبدلهای روغن هیدرولیک گیربکس و یاتاقانها است. آسیاب گلولهای از یک استوانه فلزی با قطر 2 الی 5 متر است که در راستای محور اصلی خود چرخش مینماید. وزن سازهای آسیاب گلولهای بسیار بالا است و بر روی دو یاتاقان قرار میگیرد. روغن هیدرولیک نقش روان کننده را دارد که بین یاتاقانها توسط فشار پمپ هیدرولیک قرار میگیرد و به دلیل گرم شدن نیاز به کاهش دما دارد. مبدل حرارتی آب – روغن هیدرولیک که عموما در آسیابهای سیمان از نوع شل تیوب یا پوسته لوله است دمای روغن هیدرولیک را در محدوده مجاز تنظیم مینمایند.
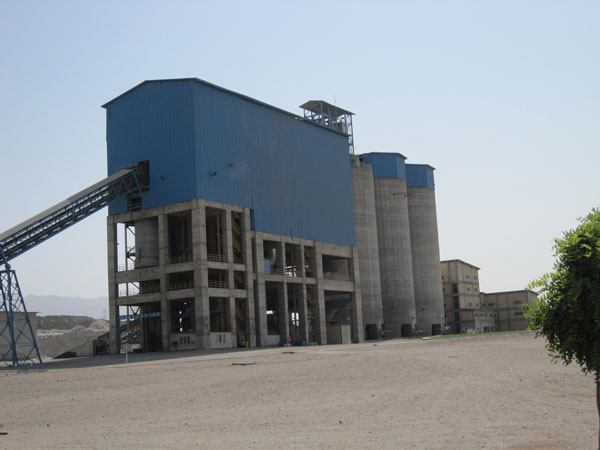
تشکیل رسوب املاح معدنی آب به ویژه کربناتهای کلسیم و منیزیم داخل لولههای مبدل باعث کاهش انتقال حرارت و افزایش دمای روغن هیدرولیک میگردند. افزایش بیش از حد دمای روغن هیدرولیک موجب توقف اتوماتیک واحد آسیاب میگردد. جهت رفع مشکل، مبدل روغن هیدرولیک میبایست اسید شویی طبق روشهای سنتی اسیدشویی گردد. اسیدشویی علاوه بر باز کردن رسوبات به فلزات نیز آسیب میرساند و درصورت اسیدشویی غیراصولی و بدون مواد اینهیبیتور، عمر مبدل به شدت کاهش مییابد. یکی از عواقب اسیدشویی، سوراخ شدن تیوبهای مسی مبدل روغن هیدرولیک و خطر نشت روغن هیدرولیک به مدار آب صنعتی و مخازن و آلوده کردن آن است. به طور متوسط حجمی معادل 3000 الی 4000 مترمکعب خطر آلودگی دارد. از سوی دیگر از دست رفتن روغن هیدرولیک است که هزینه آن نیز بسیار بالا است. تصویر ذیل، میزان رسوبات و خوردگی را در داخل مبدل حرارتی روغن هیدرولیک در آذرماه 1390 همزمان با نصب رسوب زدای هیدروفلو نشان میدهد.
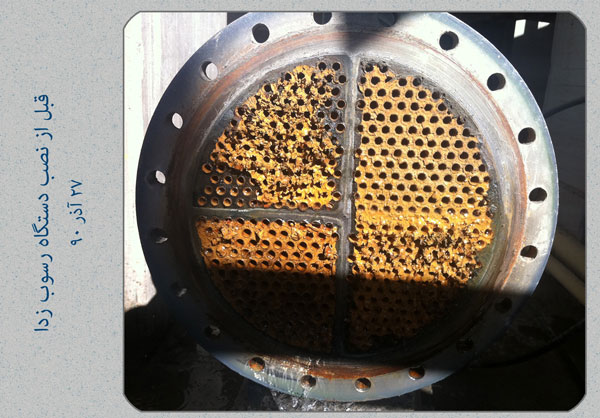
در آذرماه 1390 بخش فنی کارخانه سیمان ممتازان کرمان نسبت به نوآوری تکنولوژی هیدروفلو ابراز علاقه کرده و دو دستگاه رسوب زدای هیدروفلو که مبتنی بر کدینگ امواج رادیویی بی ضرر باند AM کار مینماید بر روی مسیر ورودی آب مبدل (پوسته-لوله) خنککن روغن هیدرولیک یونیت ورودی آسیاب سیمان (5411LQ1) نصب نمودند. پس از نصب رسوب زا به دفعات بازدیدهایی که عمدتاً چشمی بودهاند از وضعیت عملکرد رسوبزدای هیدروفلو انجام گردید. تقریباً از 3 ماه پس از نصب سختی گیر تأثیراتی در باز نمودن رسوبات و کاهش محصولات خوردگی مشاهده گردید. نکته قابل توجه باز بودن اکثر تیوبها و نرم بودن رسوبات هستند. تصاویر ذیل که در تصاویر ضمیمه مشهود است.
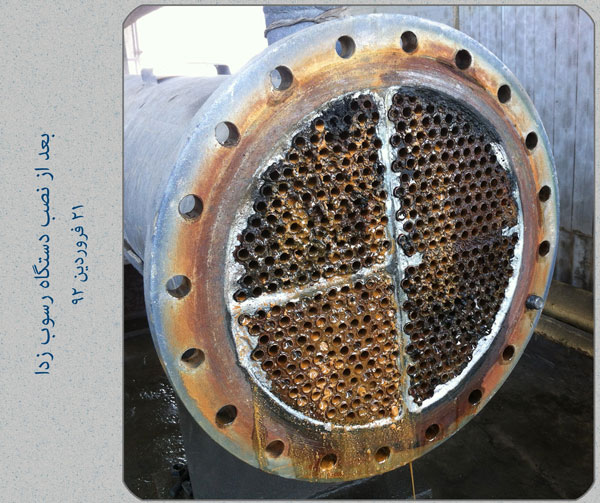
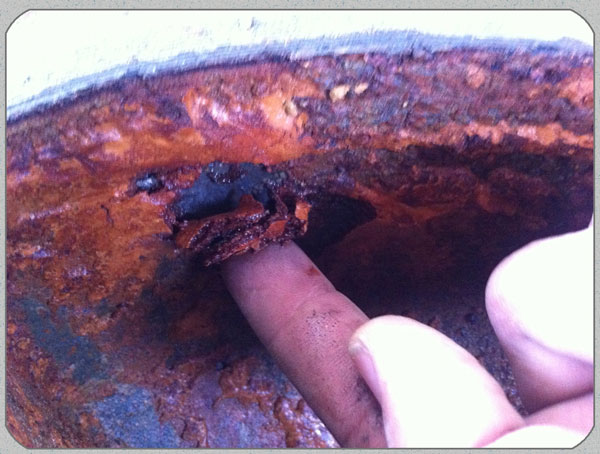
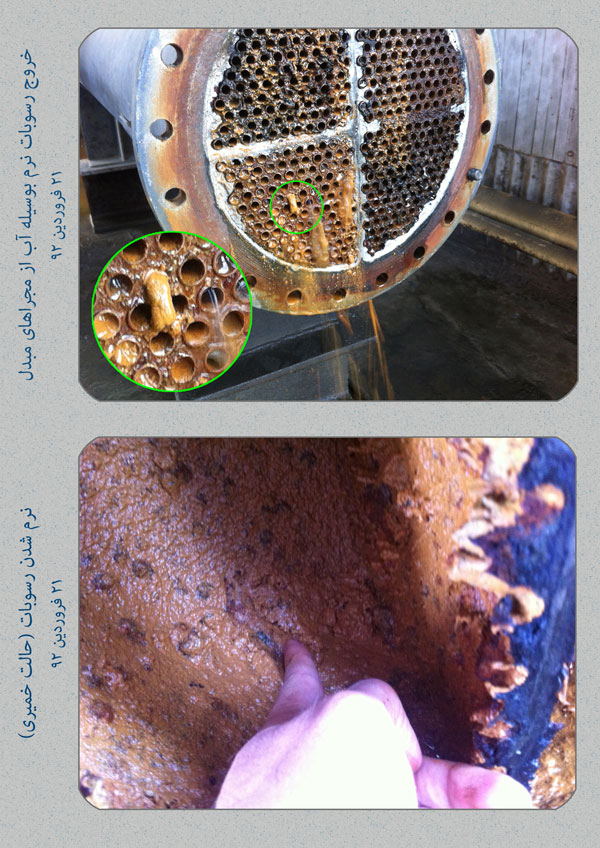
با توجه به گذشت بیش از 7 سال از زمان نصب میتوان گفت که این سیستم میتواند رسوبات سخت بهجامانده که پیشتر با استفاده از مواد شیمیایی، اسیدشویی و روشهای فیزیکی به وسیله تجهیزات تمیزکاری برطرف میشدند، به شکل نرم و خمیر گونهای درآورد که با شستشو با آب از سیستم خارج میشوند. در حال حاضر خرید و تعویض یک مبدل صفحههای ساخت آلمان یا مبدل هیدرولیک روغن بیش از 600 میلیون تومان هزینه در بردارد. تکنولوژی رسوب زدایی هیدروفلو بهترین محافظ تجهیزات حساس کارخانجات صنعتی است که بدون نیاز به سرویس و نگهداری بوده و عمری بیش از 35 سال دارد. مصرف برق ناچیز 35 وات، عملاً هزینههای بهره برداری رسوب زدای هیدروفلو را در مقایسه با سایر روشهای سختی گیری به ویژه سختی گیر رزینی و یا سیستم فیلتراسیون صنعتی RO صفر است.
همچنین واحد فنی پیشنهاد داده که با اولویت بندی، بخشهای مختلف از قبیل آب خط تولید و موتورخانههای ساختمانهای جنبی بهاین دستگاهها مجهز شوند تا بتوان مشکلات موجود در زمینه رسوب و گرفتگی در سیستمهای پاپینگ و تجهیزات را به حداقل رساند.
نصب رسوبزدای هیدروفلو در شرکت توزیع برق KOE
در روسیه و کشورهای استقلال یافته از شوروی سیستم گرمایش مرکزی در شهرها بسیار رایج بوده و کماکان مورد بهره برداری قرار میگیرند. کشور اوکراین نیز از این قاعده مستثنی نیست. در قسمتی از شهر کیف، شهرداری موتورخانه فرعی را برای تامین گرمایش بخشی از شهر در نظر گرفته است. منطقه Darnitsa توسط شرکت توزیع برق KOE اداره میگردد. در این موتورخانه فرعی مبدلهای حرارتی پوسته لوله نصب شده که بخار در قسمت پوسته به عنوان سیال گرم کننده و آب داخل تیوبها به عنوان سیال گرم شونده در جریان است.

قبل از نصب رسوبزدای هیدروفلو، به طور معمول هر 3 الی 5 ماه مبدلها باز و رسوبات داخل تیوبها تمیز میشدند.
طبق بررسی کارشناسان رسوبات داخل مبدل ترکیباتی از املاح کربنات کلسیم، منیزیم، زنگار آهن و محصولات خوردگی و همچنین بایوفیلم بوده که راندمان انتقال حرارت مبدلها را به شدت کاهش میداده است. پس از بررسیهای انجام شده توسط نماینده اوکراین یک دستگاه رسوبزدای هیدروفلو مدل I-100 جهت رفع مشکل رسوب و خوردگی و بایوفیلم در اول سپتامبر 2017 بر روی ورودی یکی از مبدلها نصب گردید که در تصویر بالا موقعیت نصب رسوبزدای هیدروفلو مشخص است.
جهت بررسی عملکرد رسوبزدای هیدروفلو بازه زمانی 1 ماهه در نظر گرفته شد.
پس از یک ماه ورودی مبدلها باز و نتایج جالب توجه ذیل مشاهده گردید.





عکس بالا گویای این است که در مدت زمان کوتاه 1 ماه از نصب رسوب زدای هیدروفلو روند مثبت رسوبزدایی کاملاً مشهود بوده به نحوی که در ابتدای تیوبها کاملاً رنگ مس مشخص و نمایان شده است.
تکنولوژی رسوبزدای هیدروفلو تنها سختی گیر الکتریکی است که دارای عملکرد واقعی و عالی است. سختی گیر هیدروفلو بر خلاف سایر سختیگیرهای موجود در بازار با استفاده از امواج رادیویی بی ضرر کار مینماید. از مهمترین مزیتهای رسوب زدای هیدروفلو حذف سختی گیرهای رزینی رایج بوده که بهره برداری از آنها بسیار وقت گیر و مشکل است.
برای استفاده بهینه از رسوبزدای هیدروفلو فقط کافیست مدل مناسب در محل مناسب نصب گردد که این بخش از کار بر عهده تیم فنی شرکت رادین گسترسینا نماینده انحصاری رسوبزدای هیدروفلو است که همواره استفاده از تکنولوژیهای مدرن و دوستدار محیط زیست را توصیه مینمایند.
رسوبزدایی برجهای خنک کن تر نیروگاه حرارتی
رسوبگذاری املاح معدنی در برجهای خنک کن
تر نیروگاهی مشکلات و هزینههای بسیاری همواره به بهرداران تحمیل
مینماید. در نیروگاه حرارتی در یکی از استانهای چین که دارای 2 واحد تولید
برق 600 مگاواتی است، مقابله با رسوب و جلبک توسط تزریق مواد شیمیایی ضد
رسوب و بایوساید انجام و آب خام برجهای خنک کن از آب رودخانه تامین
میگردد. کیفیت آب رودخانه بنام yuen باتوجه به فصول سال متغیر بوده و
کدورت آب در زمان بارندگی فصلی تابستانی بسیار افزایش مییابد.
در هفتم نوامبر سال 2016 دو دستگاه رسوب زدای هیدروفلو مدل HydroFlow
Custom 72” بر روی لولههای خروجی پمپها با قطر 1800 میلیمتر با هدف کاهش
مواد شیمیایی ضد رسوب و جلبک نصب گردید.


در زمان نصب رسوبزدای هیدروفلو در نوامبر
2016، واحد 1 در مدار و در حال بهره برداری بود و تزریق مواد شیمیایی 1
هفته بعد از نصب سختی گیر هیدروفلو متوقف گردید.
واحد دوم در 21 ژانویه 2017 (حدود 5/2 ماه بعد) در مدار قرار گرفت با
بررسی سوابق دما در نقاط مختلف سیکل ، اختلاف دمای آن آب خروجی کولینگ از
کندانسور و دمای بخار کندانس شده 5 الی 6 درجه سانتیگراد در زمان مشابه
سال قبل بوده است. بعد از نصب سختیگیر هیدروفلو علی رغم حذف مواد شیمیایی و
افزایش انتقال حرارت این اختلاف دما به 4 الی 5 درجه سانتیگراد کاهش یافته
است. یعنی عملاً دمای کندانس خروجی به دمای آب کولینگ خروجی نزدیک شده که
نشان دهندهی انتقال حرارت بهتر است.

در تاریخ 23 مارچ 2017 کندانسور واحد 1 جهت
بازدید باز گردید. داخل تیوبهای کندانسور هیچگونه رسوب سفت مشاهده نگردید.
کلیه رسوبات به صورت رسوبات نرم دیده شد که به راحتی توسط شستشو با اب تمیز
میگردد.
با توجه به وضعیت بسیار عالی مشاهده شده نیروگاه تصمیم گرفت که واحدها را تا زمان اورهال در نوامبر سال 2017 در مدار قرار دهد.

با استفاده از رسوبزدای هیدروفلو نتایج ذیل حاصل گردید:
1- تزریق مواد ضد رسوب کاملاً متوقف گردید.
2- رسوبات سخت در داخل کندانسور و برج های خنک کن مشاهده نگردید.
3- انتقال حرارت در کندانسور به میزان 5/1 درجه سانتیگراد بهبود یافت.
4- آب خروجی بلودان برج های خنک کن در آبیاری فضای سبز مورد استفاده قرار
گرفت که این امر بدلیل حذف مواد شیمیایی از آب برج خنک کن بوده است.
در صنایع خودرو سازی هوای فشرده از ارکان مهم در خطوط تولید است. به همین منظور کمپورسورهای هوای فشرده در فضایی به نام کمپرسورخانه یا COMPRESSOR مستقر میشوند. کمپرسورها دسته بندیهای مختلفی دارند که مهمترین آنها OIL FREE یا OIL INJECT همچنین دارای مدار هوا خنک یا آب خنک است.
در کارخانه ایران خودرو دیزل بخش کمپرسورخانه دارای 2 مجموعه کمپرسور هوای فشرده اویل فری و اویل اینجکت است که هردو مجموعه با آب خنک میگردد.
بعد از نصب موفقیت آمیز 1 دستگاه رسوبزدای هیدروفلو در بخش هیدرو تست یا آزمایش نشتی آب اتوبوس مدیریت فنی تصمیم گرفت تا از این تکنولوژی نوین و موثر در رفع مشکل رسوب در مدار خنک کنندگی و برجهای خنک کن کمپرسورها استفاده نمایند.
در سال 1387 پس از بازدید فنی، 1 دستگاه رسوبزدای هیدروفلو مدل P-160 بر روی کمپرسورهای اطلس کوپکو OIL FREE نصب گردید. واحد OIL FREE شامل 5 دستگاه کمپرسورهای اطلس کوپکو مدل ZR250 است.


رسوبزدای هیدروفلو با طراحی صنعتی و عمر مفید بیش از 35 سال بهترین جایگزین سختی گیرهای رزینی میباشند که معایب سختی گیرهای رزینی نظیر نیاز به اسیدشویی دوره ای و خوردگی لوله ها را نیز ندارند.
رسوبزدای هیدروفلو با استفاده از فریتهای بسیار خاص و غیرقابل کپی برداری، سیگنالهای ایمن رادیویی را به کل مدار لوله کشی القا مینماید.

حذف سختی گیر رزینی عملیات و تکثیر احیا و بکواش را حذف نموده و پساب نمکی آلوده نیز به محیط زیست و آبهای زیرزمینی وارد نماید. برخلاف سختی گیرهای رزینی، رسوبزدای هیدروفلو قادر است رسوبات قدیمی را حذف نموده و از تشکیل رسوب جدید جلوگیری نماید. بنابراین نیاز به اسید و اسیدشویی حذف میگردد.
در این پروژه ایران خودرو دیزل پس از نصب رسوبزدای هیدروفلو سختی گیر رزینی از مدار خارج گردید به مدت 2 ماه رسوبات باز شده در صافیها، برجهای خنک کن جمع آوری گردید مدار خنک کننده کمپرسورهای اطلس کوپکو که شامل اویل کولر یا مبدل روغن، اینتر کولر، افتر کولر، مدار خنک کننده ژاکت استیج1 و استیج 2 است که از لحاظ فرایندی بسیارپیچیده و تودرتو با سیستم های کنترلی است که نسبت به رسوبگذاری بسیار مستعد است.
همچنین در کولرهای هوا آب در پوسته مبدل حرکت میکند که امکان رسوبگزاری بسیار بالاتر از تیوبها است. باتوجه به تمامی پیچیدگیهای اشاره شده در بالا، علی رغم حذف سختی گیر رزینی مواد ضد رسوب و آنتی اسکالانت بیش از 11 سال بدون رسوب و رسوب گذاری در لولههای آب خنک کن، مبدلهای حرارتی، ژاکت موتور کمپرسورها، بدنه استیج 1 و2 کمپرسور با افتخار در حال بهره برداری است.
نصب رسوبزدای هیدروفلو در کارخانه سیمان اردستان
کوره دوار اصلیترین قسمت هر کارخانه سیمان و قلب مجموعه است. کوره به صورت دوار طراحی شده و مواد خام از یک سو وارد کوره شده و پس از پخته شدن مواد از سمت دیگر کوره به شکل کلینکر وارد گریت کولر میشود. وزن کوره بسیار زیاد است که عموما بر روی 2 الی 3 پایه اصلی بتنی، یاتاقانها نصب میشوند. دمای کوره بسیار بالاست و انتقال حرارت به صورت تابشی و در بخش یاتاقانها حرارت به صورت هدایتی به یاتاقانها منتقل میگردد.

سرعت حرکت چرخشی کوره بسیار پایین است و یاتاقانهای کورههای دوار به صورت هیدرودینامیکی شافت هرزگرد یاتاقان را روانکاری میکند. جهت کاهش دمای یاتاقانها داخل بدنه فلزی یاتاقان خالی بوده و دارای مدار گردش آب خنک کن است. عموما سایز لوله ورودی یاتاقانها ¼1 اینچ است و مجموعه 1 یاتاقان کوره دارای 4 ورودی آب خنک کن است. بخش دیگری از آب مبدلهای هیدرولیک یا روغن گیربکس کوره را خنک میکنند. در سال 1389 واحد تاسیسات کارخانه سیمان اردستان جهت حل مشکل رسوب با شرکت رادین گستر سینا تماس گرفتند. علی رغم مدت زمان کم بهرهبرداری لایههای رسوب در خطوط برگشت یاتاقانهای کوره کاملا مشهود بود.
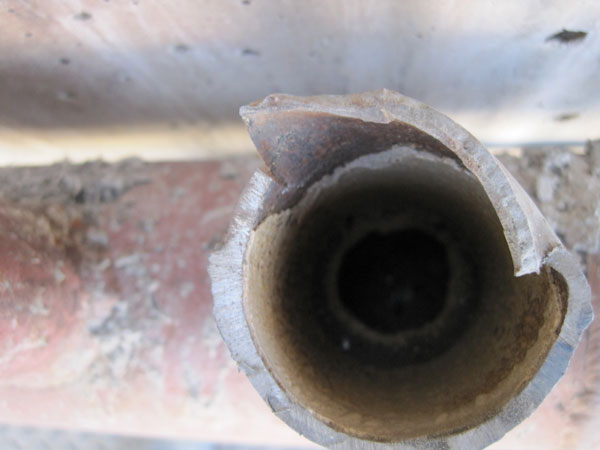
کوره کارخانه سیمان اردستان دارای 2 پایه کوره است. مبدلهای حرارتی گیربکس نیز بر روی پایه خروجی(پایه شماره 2) نصب هستند.
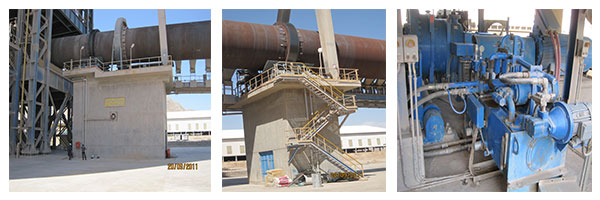
در شهریورماه سال1390 دو دستگاه رسوبزدای هیدروفلو جهت حفاظت مدار یاتاقانهای کوره و مبدلهای حرارتی گیربکس بر روی مدار آب خنک کن نصب گردید. با توجه به سابقه شرکت رادین گستر سینا در کارخانجات سیمان جهت پروژههای مختلف با در نظر گرفتن سختی آب و شرایط موجود در سایت مدلهای متفاوتی ارائه میگردد تا بهترین راندمان رسوب زدایی را به همراه داشته باشند.
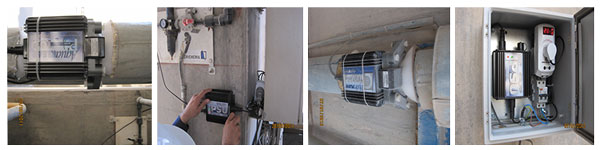
بازدیدهای دورهای جهت کنترل عملکرد رسوب زدایی در سال های 1391،1392،1394،1395 صورت گرفت. تصاویر ذیل داخل صافی برنجی را نمایش میدهد که فاقد هرگونه رسوب و خوردگی در سال 1394 است همچنین صافی داخل استرینر نیز که از جنس استیل است کاملا تمیز و فاقد رسوب چسنده است.

رسوبزدای هیدروفلو حدود 7 سال در فضای آزاد نصب و بدون مشکل یاتاقانها و مبدلهای گیربکس را در مقابل رسوب و خوردگی محافظت کردهاند. عمر رسوب زدای هیدروفلو بیش از 30 سال است و مجموعه فنی شرکت سیمان اردستان از عملکرد رسوبزدای هیدروفلو رضایت داشتهاند.
حل مشکل رسوب در سیستم تزریق آلومینیوم دایکست

Murcott یک کارخانه قالبسازی دایکست آلومینیوم واقع در Tomworth انگلستان است. زمینه فعالیت آن شامل طراحی، توسعه و تولید قالبهای پیچیده و دقیق است. مشتریان این کارخانه شرکتهای بزرگی مانندNike BMW، IBM، جگوار، رولزرویس و موتورسیکلتهای Triumph است که همگی نیازمند بالاترین استانداردها هستند.
مشکل : با توجه به سختی بالای آب منطقه، رسوب همواره در این کارخانه به ویژه در قسمت خنک کن قالبها دردسرآفرین بوده است. آب سرد با فشار ناشی از پمپهای مدار خنک کننده، از قالبهای داغ و از میان مسیرهای نسبتا باریک عبور میکند. در این شرایط امکان تشکیل رسوب و بسته شدن این مسیرها بسیار بالا بوده که این امر منجر به افزایش دمای قالبها میگردد. تنها راهکار مورد نظر آلن بلیک، مدیر نگهداری و تعمیرات کارخانه، تعویض کلیه قالبها دو بار در سال بوده است. دستگاههای تزریق آلومینیوم دایکست هر کدام وزنی بین 10 تا 20 تن داشته و دارای 6 تا 8 قالب بودند. به منظور پاکسازی مجاری عبور آب از رسوبات میبایست دستگاهها خاموش، و قالبها را بیرون کشیده و مسیر اولیه قالبها جهت تخلیه رسوب توسط مته سوراخ گردد سپس با اسید مجاری، رسوبزدایی میگردد. تنها بیرون کشیدن قالبها 7 تا 8 ساعت به طول میانجامد و سوراخ کردن مسیرها نیز به 15 دقیقه زمان نیاز دارند. پس از آن نیز 7 تا 8 ساعت دیگر مورد نیاز است تا تمام قطعات را مونتاژ نموده و دستگاههای تزریق را مجددا راه بیندازند.
مشکل دیگر در کارخانه، برجهای خنک کن بود. در این برجها نه تنها مشکل رسوب بلکه مشکل آلودگی میکروبی - لژیونلا نیز وجود داشت. میزان لژیونلا به طور معمول طبق اندازه گیریهای دوره ای 103 بوده اما زمانی که این مقدار به 106 میرسید با یک شوک کلر به میزان 3 لیتر هیپوکلریت سدیم این مشکل بر طرف میگردید. تزریق بیش از حد هیپوکلریت سدیم نیز، خطر خوردگی داخل لولهها را به همراه داشت. همچنین برجهای خنک کن را نیز میبایست دو بار در سال از مدار خارج کرده و رسوبات را از پکینگها و سطوح داخلی میزدودند که این عمل همراه با پروسه خارج کردن رسوبات از برجهای خنک کننده بیش از 3 ساعت به طول میانجامید.
راه حل :در تابستان 2005 آلن بلیک تحقیقات خود با تکنولوژی نوین رسوبزدایی را آغاز و نهایتا با شرکت هیدروپت آشنا شد و از آنجا که گزارشات بیانگر نتایج مثبت عملکردی تکنولوژی بود، تصمیم میگیرد با شرکت هیدروپت ارتباط برقرار کند. پس از یک سری مذاکرات، مدیر عامل شرکت هیدروپت، دکتر دنیل استیفانینی استفاده از دستگاه رسوب زدای مدل P-120 را پیشنهاد نمودند. در ژوئیه سال 2005 یک دستگاه رسوبزدای هیدروفلو مدل P-120 جهت محافظت از خطوط تولید و برجهای خنک کن مرتبط به آن، نصب شد. تنها همین یک دستگاه قابلیت محافظت از کلیه دستگاههای تزریق آلومینیوم دایکست را داشته است.
نتایج : زمان نصب دستگاههای AquaKlear، قالبها را تمیز نمودند. حدود 6 ماه بعد، سیستم مورد بازبینی قرار گرفت. آلن تحت تأثیر نتیجه عملکرد تکنولوژی قرار گرفت، چرا که هیچ نوع رسوبی در قالبها وجود نداشته و در برجهای خنک کن نیز رسوبی به چشم نمیخورد. زمان شستشوی برجها که پیش از نصب دستگاه 3 ساعت به طول میانجامید، پس از نصب دستگاه کمتر از یک ساعت زمان نیاز داشت. از فواید دیگر استفاده از دستگاه، حل مشکل لژیونلا بود. دلیل اصلی استفاده از دستگاه سختیگیر هیدروفلو مشکل لژیونلا نبوده اما از آنجا که سختیگیر هیدروفلو باعث از بین رفتن باکتریها میشود، مقدار لژیونلا نیز به طور چشمگیری از 103 به 101 کاهش یافت که در این سطح از لژیونلا از لحاظ جنبههای ایمنی و سلامتی قابل قبول است. در نتیجه عملکرد موفق دستگاه هیدروفلو، مدیران کارخانه را بر آن داشت که از یک دستگاه برای یک برج خنک کن دیگر و همچنین برای ماشینهای تزریق قدیمیترشان استفاده کنند. آلن اذعان میدارد، " در ابتدا من نسبت به عملکرد دستگاههای هیدروفلو مطمئن نبودم اما در پایان نتیجه آن مرا شگفت زده کرد. با استفاده از این دستگاه بسیاری از مشکلات عمده ی تولید و نگهداری از بین رفته و در هزینه و زمان صرفه جویی شده است. علاوه بر این میزان مصرف مواد شیمیایی که جهت از بین بردن لژیونلا مورد استفاده قرار میگرفت نیز کاهش پیدا کرد که این امر به نوبه خود فواید زیادی برای محیط زیست دارد.

نصب رسوبزدای هیدروفلو در در کارخانه Rozhy Schenskyy اکراین
در کارخانه Rozhy Schenskyy اکراین که تولید کننده پنیر است، مشکل
رسوبات معدنی و پروتئینی در مبدلهای صفحهای استیل و ممبرانهای فیلتراسیون
Uf وجود دارد.
هدف از نصب دستگاه رسوبزدای هیدروفلو بر روی سیستم فیلتراسیون UF، حذف رسوبات آلی و بایوفیلم در مبدلهای صفحهای،
از بین بردن باکتریهای بیماری زا E-coli و سایر میکروارگانیسمها است و
همچنین کاهش مصرف مواد شیمیایی در فرایند شستشوی CIP است. این آزمایش در
مدت حدود 1 ماه از ژوئن 2018 و ژولای 2018 انجام پذیرفته است.
آب پنیر جهت جداسازی آب و مایه پنیر وارد دستگاه فیلتراسیون Uf میگردد.
سایز لوله ورودی "4/11 است که یک دستگاه رسوب زدای هیدروفلو بر روی آن
تعبیه شده است در این شرکت آب تصفیه شده برای سیستم پرکن برج خنک کن
استفاده میشود همچنین مایه پنیر خروجی از دستگاه فیلتراسیون UF جهت تولید
شیرخشک مورد استفاده قرار میگیرد.

به طور معمول مبدل صفحهای روزانه 12 الی 14 ساعت در مدار قرار میگیرد. قبل از نصب رسوبزدای هیدروفلو، انتقال حرارت و دما در مبدل حرارتی کاهش
یافته و متعاقباَ مبدل صفحهای نیاز به باز کردن و تمیز کردن رسوبات آلی و
پروتئینی پیدا مینماید. در این مدت فرایند تولید متوقف میگردد.

در روز نصب سختی گیر هیدروفلو با هماهنگی تیم
فنی کارخانه مبدلهای حرارتی باز و وضعیت رسوبات بیولوژیکی و بایوفیلم پس
از دوره ی تیم کاری 14 روزه مشاهده گردید.

کلیه صفحات مبدل تمیز شده و با روشن کردن سختیگیر هیدروفلو که نیاز به
برق 220 ولت با توان 25 وات دارد، سیگنالهای ایمن و تاثیرگذار هیدروفلو در
تمامی مدار لوله کشی فیلتراسیون UF توزیع گردید. بعد از گذشت 14 روز از
عملکرد رسوبزدای هیدروفلو تیم فنی مشکل افت دما و کاهش انتقال حرارت
نداشتند و نیازی به بازکردن مبدل صفحه ای نبود. فرآیند تولید بدون توقف و
بدون کاهش انتقال حرارت تا 36 روز انجام شد. در روز 36ام جهت بررسی عملکرد
رسوب زدای هیدروفلو مبدلهای صفحهای مونتاژ و باز شدند، در کمال تعجب
هیچگونه رسوب معدنی، آلی و بیولوژیکی بر روی صفحات مبدل مشاهده نگردید.

در نهایت تیم فنی کارخانه اذعان داشتند که در طول مدت 36 روز بهره
برداری با رسوبزدای هیدروفلو در سیستم فیلتراسیون UF و مبدلهای صفحهای
هیچگونه رسوب بیولوژیکی و بایوفیلم تشکیل نشده است.
مبدلهای صفحهای نیازی به توقف سیستم جهت تمیز کردن ندارند. تعداد
میکروارگانیسمهای مزوفیلی یا تخمیری بی هوازی بیش از 2 برابر کم شده است.
همچنین مقدار پسآب تولیدی سیستم فیلتراسیون نیز کاهش قابل ملاحظهای داشته
است. رسوب زدای هیدروفلو با جنسی بسیار ساده و بدون توقف و برش لوله قادر
است سیگنالهای رادیویی ایمن در مدار لوله کشی ایجاد کند که علاوه بر
رسوبات معدنی رسوبات آلی و پروتئینی و بایوفیلم را نیز کنترل و حذف
مینماید.
تصاویر ذیل نیز قبل و بعد ورودی مبدل صفحه ای را نمایش میدهد.

تکنولوژی رسوب زدایی هیدروفلو در کارخانه فرآوردههای لبنی تایمز
کارخانه فرآوردههای لبنی تایمز واقع در باکینگهام شایر، با بکارگیری تکنولوژی رسوبزدایی هیدروفلو صرفه جویی قابل توجهی در مصرف مواد شیمیایی CIP، زمان توقف خط تولید و میزان شیر هدر رفته ناشی از ایجاد رسوبات آهکی و شیر در مبدلهای حرارتی، نموده است. این کارخانه که تولید کننده فرآوردههای لبنی مانند ماست و خامه است، در ناحیهای با آب بسیار سخت واقع شده است. اخیراً به منظور مقابله با این مشکل، از چند دستگاه رسوبزدای الکترونیکی هیدروفلو در سه بخش از این کارخانه برای کنترل رسوبات آهکی منابع تغذیه آب و از یک دستگاه هم در خط تولید شیر قبل از مبدل حرارتی استفاده شد.
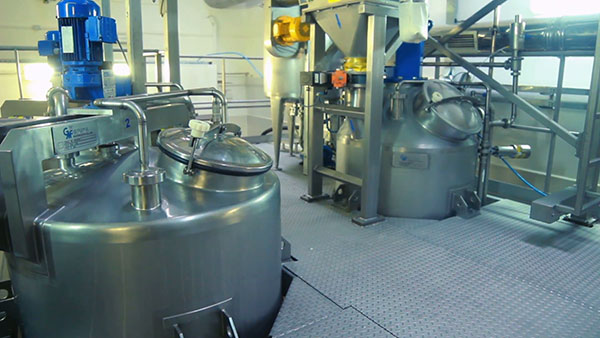
یک دستگاه رسوبزدای هیدروفلو مدل C45 در خط تولید شیر نصب گردید. قبل از نصب رسوبزدای هیدروفلو، اپراتورها میبایست دو بار در هفته خط تولید را متوقف کرده و آن را با اسید فسفریک تمیز کنند. بعد از نصب رسوبگیر هیدروفلو، تنها یک بار در هفته نیاز به پاک سازی و CIP خط تولید است. علاوه بر افزایش تولید، میزان اسید فسفریک لازم برای اسید شویی CIP حدود 50 درصد کاهش یافت.
رسوبگیر الکترونیکی هیدروفلو، یک دستگاه اصلاحگر فیزیکی آب است که از ایجاد رسوبات آهکی شامل کربنات کلسیم و منیزیم جلوگیری میکند. نحوه کار این دستگاه، انتشار میدان الکتریکی با فواصل زمانی متغیر در طول لوله است. این میدان الکتریکی با ایجاد خوشههای یونی معلق در آب که به عنوان هستههای کریستالهای معلق عمل میکنند باعث میشود که بی کربناتهای محلول به جای رسوب گذاری بر روی سطح به شکل کریستالهای معلق و غیر چسبنده تبدیل شوند. بنابراین کریستالهای معلق، به لوله یا سطوح مبدلهای حرارتی نمیچسبند و با جریان سیال از محل خارج میشوند.
از مزایای خاص این سیستم برای مثال، تأثیر این دستگاه بر دو طرف مدار لوله کشی است. علاه بر این، دستگاه بر آب ساکن (بدون جریان) نیز تاثیر داشته و محدود به آب عبوری از محل دستگاه نیست. دستگاه سختیگیر هیدرفلو هم بر روی سیستمهای قدیمی و هم سیستمهای جدید قابل نصب است و به دلیل هزینههای عملکردی بسیار پایین در مدت زمان کوتاهی هزینه خرید جبران خواهد شد. این دستگاه برای محیط زیست هم فوایدی مثل کاهش مصرف سوخت و انرژی و عدم شور نمودن پساب ناشی از سختی گیرهای رزینی را در بر خواهد داشت.
پروژههای مرتبط در زمینه مبدلهای حرارتی:
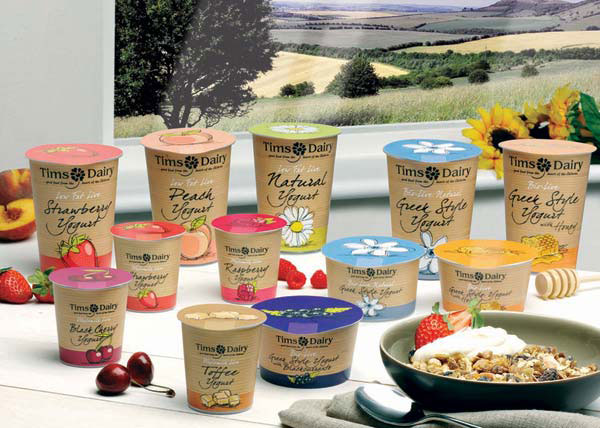
مجتمع پتروشیمی شازند یکی از طرح های زیر بنایی و مهم کشور می باشد که در راستای سیاستهای کلی توسعه صنایع پتروشیمی و با اهداف تامین نیاز داخلی کشور و صادرات ایجاد و به بهره برداری رسیده است .پتروشیمی اراک در جوار پالایشگاه هفتم ، واقع در کیلومتر 22 جاده اراک-بروجرد ودر زمینی به مساحت بالغ بر 523 هکتار احداث گردیده است . این مجتمع مشتمل بر 17 واحد تولیدی ، به انضمام واحد های سرویس های جانبی و آفسایت می باشد و محصولاتی نظیر پلی اتیلن سنگین، پلی اتیلن سبک خطی،پلی پروپیلن و پلی بوتادین رابر تولید می نماید .
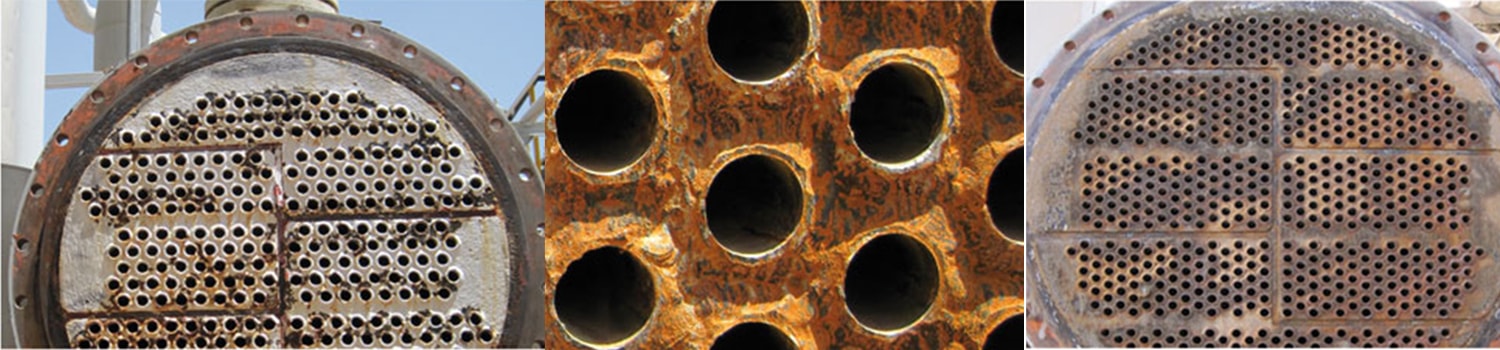
نصب اول :
پس از برگزاری سمینار آشنایی با تکنولوژی هیدروپت در مهر ماه 1387 مقرر گردید یک دستگاه رسوب زدای الکترونیک هیدروپت سری HydroFlow مدل C-EX 160 ضد انفجار زون یک-کلاس یک بر روی لوله خنک کن ورودی مبدل H-70 1A,B واحدLLDP نصب گردد . در این مبدل ها آب خنک کننده در قسمت پوسته جریان دارد .سابقه رسوبگذاری در این مبدل هر 2 ماه یک بار بوده ، به نحوی که به دلیل کاهش انتقال حرارت مبدل اول از مدار خارج و اسید شویی می گردیده و متعاقباً مبدل دوم وارد سرویس می شده است . مقرر گردید پایلوت عملکرد دستگاه در مدت سه ماه انجام گردد .بعد از سه ماه مبدل با عنایت به انتقال حرارت بسیار خوب از مدار خارج نگردید و کارشناسان مجتمع درخواست افزایش دوره 3 ماهه به 5 ماه را نمودند تا بررسی های بیشتری انجام گردد . پس از 5 ماه و بررسی های تیم بهره برداری نیازی به جابجایی مبدل ها تشخیص داده نشد و تائید نهایی دستگاه منوط به باز شدن مبدل و تاییدیه بازدید چشمی گردید . نهایتاً پس از 8 ماه از نصب و توقف تولید ، شرایط برای بازدید محیا گردید . علی رغم اینکه در این مدت مبدل در سرویس نیازی به اسید شویی پیدا ننموده و با مبدل رزرو تعویض نگردیده مقرر گردید تست جدیدی بر روی مبدل دیگر انجام گردد .
متعاقباً رسوب زدایی الکترونیکی هیدروپت به واحد PBR/BD (بوتادین سبک و سنگین) منتقل و بر روی ورودی خط خنک کننده مدل 175 نصب گردید . پس از گذشت چهار ماه و کنترل شرایط پروسسی در اتاق کنترل روند مثبت دستگاه مشهود بود .
نصب دوم:
تیم بهره بردار واحد بوتادین درخواست نصب دستگاه جدیدی را می نماید . پس از بررسی های فنی یک دستگاه رسوبزدای الکترونیک هیدروپت سری HydroFlow مدل C-EX-160 ضد انفجار زون یک – کلاس یک بر روی لوله ورودی مبدل 102 نصب گردید .
مبدل 102 یک مبدل پوسته لوله می باشد که سیال پروسسی با دمای 70درجه سانتیگراد وارد پوسته مبدل می گردد. آب خنک کن توسط لوله 6 اینچ وارد تیوب های مبدل شده و سیال پروسسی را تا دمای 40 درج سانتیگراد خنک می نماید . جهت کنترل دمای سیال پروسسی خروجی از یک شیر سه راهه موتوری در ورودی اب خنک کن استفاده گردیده که کنترل خود را از دمای خروجی می گیرد و همواره با کاهش یا افزایش درصد باز شدن شیر دمای سیال پروسسی را در 40 درجه سانتیگراد تنظیم می نماید . پس از نصب دستگاه یک مبدل حرارتی دیگر با شرایط پروسسی مشابه به عنوان سیستم شاهد در واحد بوتادین در نظر گرفته شد . پارامترهای دمای ورودی و خروجی سیال و آب خنک کننده و همچنین درصد باز شدن شیر برقی روزانه در چندین نوبت برای دو مبدل به صورت جداگانه ثبت گردید .
درصد باز بودن شیر کنترلی مبدل شاهد پس از مدت چند هفته از 15 درصد افزایش یافته و در مدت دو ماه به 105 درصد می رسد. مبدل حرارتی قادر به خنک نمودن سیال پروسسی نداشته و مبدل جایگزین وارد سرویس می گردد . اما در مبدل 102 که دستگاه رسوب زدای هیدروپت بر روی آن نصب شده است در صد باز شدن شیر کنترلی پس از دو ماه حدود بین 19 الی 22/5 درصد در نوسان بوده و افزایش بیشتری نداشته است .
چهار ماه بعد از نصب :
پس از حدود چهار ماه از نصب دستگاه شرایط کماکان تغییر ننموده و مبدل ها در زمان تعمیرات اساسی کلیه واحد های مجتمع باز و بازدید می گردند. کارشناسان بهره برداری واحد PBR/BD B حتی اعلام نمودند که در این مرحله نیز نیازی به باز کردن مبدل و بازدید آن به دلیل کارکرد خوب آن نمی دیدند ولی به دلیل ارائه گزارش به مدیران واحد و تایید فنی این دستگاه مجبور به باز کردن مدل 102 شدند .
نتیجه :
در جمع بندی نظرات واحد بازرسی فنی و بهره برداری واحد بوتادین اشاره گردید که عملکرد دستگاه در این مبدل بسیار خوب ارزیابی گردیده و اثری از رسوبات آهکی و مشکلات ناشی از آن ، از تاریخ نصب وجود نداشته است . از موارد دیگر می توان به کارکرد و راندمان بالای سیستم بعد از نصب دستگاه انجام پروسه تولید بدون توقف و بدون مشکل با بازده بسیار خوب ، افزایش قابلیت و اطمینان سیستم از نحوه کارکرد آن با نصب دستگاه ، کم شدن زمان تعمیر و نگهداری ، کاهش نیروی انسانی برای تعمیرات ، حفظ دستگاه های و مبدل برای مدت طولانی تر ، جلوگیری از ایجاد رسوبات آهکی در لوله اشاره نمود .
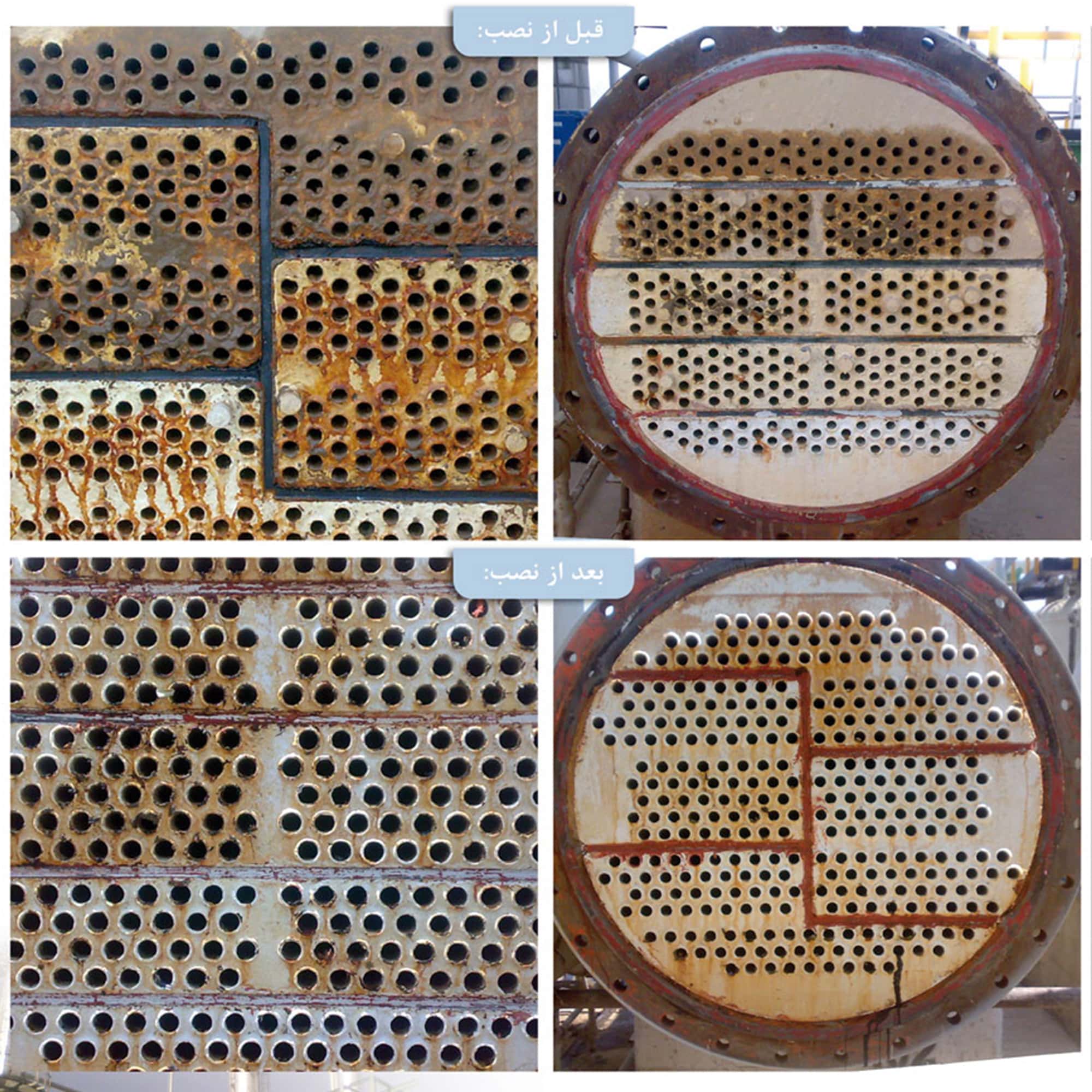
لازم به توضیح است که رنگ سفید مربوط به پوشش اپوکسی محافظتی صفحه و تیوب های ورودی مبدل حرارتی می باشد.
شرکت پتروشیمی مارون در سال 77 برای اجرای هفتم الفین با ظرفیت تولید سالانه 1/1 میلیون تن پلی اتیلن که در زمره بزرگترین الفینهای جهان است، در زمینی به مساحت 93 هکتار در سایت 2 منطقه اقتصادی بندر امام تاسیس شد. تولیدات این شرکت در منطقه ویژه اقتصادی پتروشیمی پلی اتیلن سنگین، پلی اتیلن پروپیلن، اتیلن اکساید، اتیلن گلایکول است.
مشکل
مبدلهای حرارتی 1021 واحد HDPE پتروشیمی مارون از نوع دو لوله یا Twin Pipe است که هر یک دارای طولی بیش از 35 متر هستند دارای یک غلاف لوله 8 اینچ است که آب خنک کننده در آن جریان دارد. از سوی دیگر هر مبدل دارای 4 افکت یا طبقه است و هر افکت بصورت دو لوله 8 اینچ موازی است. انتقال حرارت در افکت چهار که مواد پروسسی با دمای بالاتری وارد آن میگردند به دلیل رسوب گذاری به سرعت افت پیدا مینماید و متعاقباً تجهیزات اندازه گیری در اتاق کنترل افزایش دمای مواد را نمایش میدهند راندمان انتقال حرارت کاهش یافته و مشکلاتی برای تولید بوجود میآید. طبق بررسی در سابقه رسوب گذاری مبدل نهایتاً هر 45 روز یکبار واحد بهره برداری به ناچار اسید شویی در حین تولید (C.I.P) انجام میدادند که هزینه ای بین 18 الی 20 میلیون تومان در بر داشت.
پس از بررسیهای به عمل آمده در خرداد ماه هشتاد و هشت جهت حل مشکل انتقال حرارت افکت چهار مبدل A 1021 یک دستگاه رسوب زدای الکترونیکی هیدروپت انگلستان سری HydroFlow مدل C-EX-8” بر روی لوله 8 اینچ ورودی افکت چهار نصب گردید. پس از گذشت دو ماه و پیگیریهای مستمر از واحد بازرسی فنی، بهره برداری واحد HDPE هیچ گونه مشکل انتقال حرارت در مبدل مذکور گزارش نگردید. به عبارت دیگر اختلاف دمای ورودی و خروجی کاهش پیدا نکرد و تقریباً ثابت بود. پس از گذشت 4 ماه این روند ادامه داشت و هیچگونه نیاز به اسید شویی و تمیز کاری شیمیایی درخواست نگردید. پس از 6 ماه شرایط کاملاً ایده آل گزارش گردید و بازرسی فنی پس از بررسیهای همه جانبه عملکرد دستگاه را مورد تائید شفاهی قرار داد. پس از هشت ماه از عملکرد دستگاه بازرسی فنی درخواست بازدید از سایر افکتهای مبدل 1021 را داشتند تا پیش بینی نصب دستگاه های جدید جهت پوشش سیگنال برای کل مبدل لحاظ گردد. پس از بازدید مجدد از محل، توسط دستگاه اسیلوسکوپ پرتابل، سیگنالها در کل سیستم لوله کشی مبدلهای دو لوله دقیقاً اندازه گیری گردید.
.jpg)
این نکته جالب بود که سیگنال دستگاه از دو طرف منتشر میگردد، از ورودی افکت چهار به کلکتور ورودی که دارای هشت ورودی است منتقل شده و در افکت سه و دو سیگنالها به وضوح دیده میشدند اما وضعیت سیگنالها در افکت یک ضعیف بود. جهت پوشش سیگنال برای کل مبدل 1021 دو دستگاه رسوب زدای الکترونیکی هیدروپت انگلستان سری Hydrolow مدل C-EX-20” بر روی لوله های ورودی و خروجی اصلی کلکتورها هر یک به سایز 20 اینچ پیشنهاد گردید. با توجه به شرایط خاص محلهای نصب دستگاههای بزرگتر با سایز 22 اینچ برای پروژه سفارش ساخت داده شد. بازرسی فنی تائید خرید دستگاههای جدید را منوط به بازرسی چشمی از وضعیت داخلی مبدلها نمود. متعاقباً در خرداد ماه 1389 پس از گذشت یکسال مبدلها باز و مورد بازدید قرار گرفتند.
تصاویر ذیل نشان دهنده عملکرد دستگاه است. در حال حاضر 2 دستگاه 22 اینچ نیز در واحد HDPE نصب و راه اندازی شده است.
.jpg)
1